An Industrial Ultrasonic Cleaner Specification Guide
The ultrasonic cleaning equipment market is expected to exhibit a 3.3% CAGR by 2027 backed by increasing global adoption of industry 4.0 (the 4th Industrial Revolution), according to a report in Fortune Business Insights™ “Industrial Ultrasonic Cleaning Machine Market” 2022 focuses on short-term and long-term trends affecting the market landscape. Industrial ultrasonic cleaners play an important role in the economy. This post will help you pick a unit that best meets your requirements.
What is an “Industrial” Ultrasonic Cleaner?
Industrial ultrasonic cleaners are defined by task, not size. Industrial sonic cleaners include bench and tabletop units all the way up to multi-gallon floor mounted units.
It’s what these units must do vs. their size that’s important. So let’s begin our specification guide.
When to Specify an Industrial Ultrasonic Cleaner
To start with, the best industrial ultrasonic cleaners are employed for tough and often long-term cleaning cycles. These units may be required to continuously operate for hours and must be designed to meet these rigorous operating conditions.
Here’s a start on points to consider:
- Type of contamination to be removed. There’s a big difference, as you can imagine, between removing coolant from machined parts and baked on residues on costly plastic injection molds.
- There are also different requirements for removing varnish deposits from a carburetor and solder residues or other contaminants from delicate printed circuit boards.
- The composition of products being cleaned. Different parameters apply to cleaning aircraft engine components and PCBs. You’ll need compatible cleaning solution and ultrasonic cleaning frequency.
- A particularly tough requirement is cleaning adhesive guns and spray paint components.
Also keep in mind these points:
- How will the parts be used after cleaning?
- How do you define ‘clean’?
- Will you be cleaning batches or individual parts?
- Component size and weight
Once you define exactly what you’re trying to accomplish the following points will help narrow down your best industrial ultrasonic cleaner equipment selection.
Industrial Ultrasonic Cleaner Tank Dimensions
Next – determine how large the parts are that you will be cleaning. Here are our suggestions:
- Measure the dimensions of largest parts you will be cleaning
- Select equipment having a tank that will accommodate them
In addition, pay attention to the dimensions of the parts or sample baskets. Baskets are discussed below.
You’ll also need to know what is called the working depth of the cleaning fluid as it relates to the size of parts you’re cleaning.
The working depth is the distance from the inside bottom surface of the basket to the surface of the liquid in a filled industrial ultrasonic cleaner tank.
This is important because parts being cleaned must be fully immersed in the liquid.
If the product specs for industrial ultrasonic cleaners do not include this information ask the manufacturer or supplier.
Add Baskets to your Industrial Ultrasonic Cleaner Spec Sheet.
When cleaning smaller parts, baskets support them in an industrial ultrasonic cleaner. They affect cleaning and sample processing efficiency and, importantly, protect tanks from damage.
Baskets with insulated handles facilitate placing and removing parts being cleaned in hot liquid. They also keep parts off the tank bottom where they suppress vibration, can damage the tank and lower cleaning effectiveness.
Some baskets hang on the tank rim; others are equipped with rubber-coated feet positioned near the corners of the tank bottom where vibration is at a minimum. Fine mesh baskets for small parts can be positioned in beakers or standard baskets.
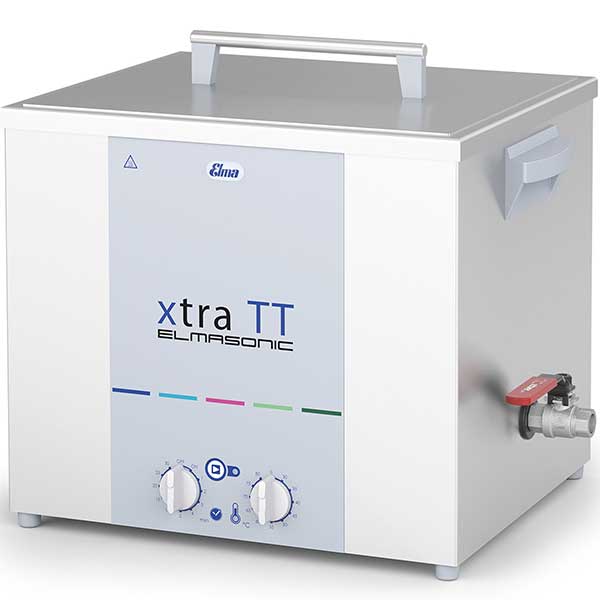
When cleaning large parts in an industrial ultrasonic cleaner an alternative to baskets is to lower the parts into the cleaning bath from overhead supports, taking care that they do not contact tank sides for bottoms. Some large models have ridges on tank bottoms on which parts can be rested during the cleaning cycle.
What Ultrasonic Frequency do you Need?
Industrial ultrasonic cleaner frequency is produced by generator-powered transducers bonded to the bottom, and sometimes to the sides of the tank. They vibrate in kilohertz (kHz or thousands of cycles per second) above the hearing range, which is approximately 20 kHz.
Most ultrasonic cleaners operate between 35 and 45 kHz. This frequency range is well suited to the vast majority of industrial cleaning tasks. An example of an industrial unit falling within this range is the Elma xtraTT series operating at 37 kHz ultrasonic frequency. These units are designed to run continuously for up to 8 hours as part of production cleaning cycles.
A lower frequency such as 25 kHz produces larger cavitation bubbles. When these bubbles implode they release a larger amount of cleaning energy. For coarse cleaning such as removal of lapping abrasives or polishing paste, a lower frequency will be more effective.
Note that the lower the frequency, the louder the cleaning operation. Sound-deadening tank lids with insulation are a good idea when operating at 25 kHz. Another useful accessory is a noise-protection box in which to place the unit.
A higher ultrasonic cleaning frequency produces smaller cavitation bubbles. These cover fine-featured complex surfaces more thoroughly and are gentler than low frequencies.
For fine cleaning of very delicate jewelry, electronics, and soft metals with polished surfaces consider a unit operating at 80 – 130 kHz.
If you are cleaning a variety of materials consider a dual-frequency industrial ultrasonic cleaner. An example is the Elmasonic xtra ST that can be set to 25 kHz for basic cleaning and to 45 kHz for fine cleaning.
Models in the TI-H series operate at 25/45 and 35/130 kHz.
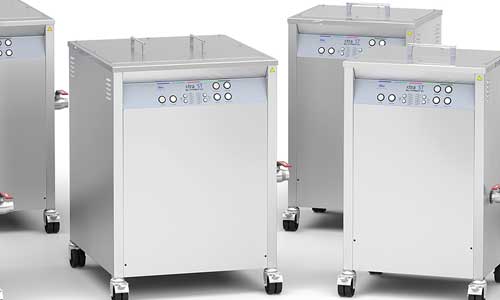
How to Manage Ultrasonic Cleaning Solution Temperature
Heat is produced by ultrasonic cavitation and many cleaning tasks are faster and more efficient when using a heated solution. For example, a heated cleaning solution is best for removing oils, machining coolants and a whole host of other contaminants associated with industrial ultrasonic cleaning.
If this is the case for your requirements you can improve throughput by using ultrasonic cleaners with thermostat-controlled heaters. But please note that above 80⁰C cavitation is inhibited and cleaning efficiency levels off.
If cleaning solution temperatures must be controlled, such as when cleaning PCBs or similar products, cooling coils will help keep bath temperatures within limits.
Cooling coils and other useful accessories are available from Elmaultrasonic.
5 Helpful Industrial Ultrasonic Cleaner Features
Industrial ultrasonic cleaning operations benefit from features available in many models. Here are brief descriptions.
1. A Degas Mode Speeds Solution Preparation
Freshly prepared ultrasonic cleaning solutions contain entrained air that inhibits cavitation.
Trapped air can be removed two ways – letting the equipment operate for a period of time without a load or specifying a cleaner with a degas mode for faster results.
A degas mode does its job by switching on and off causing air bubbles to coalesce, rise to the surface and burst. The benefit of a degas mode increases with the cleaning solution capacity of the ultrasonic cleaner’s tank.
2. The Benefits of the Sweep Mode
Sweep provides a slight ± fluctuation in the industrial cleaner’s ultrasonic frequency and serves to even out the cleaning action. This avoids what are called
- “Hot spots” or more intense and possibly damaging cavitation action
- “Dead zones” or no cleaning action, and
- Harmonic vibrations that can damage delicate parts such as PCBs.
3. The Pulse Mode Boosts Ultrasonic Power
If you are cleaning products with particularly tenacious contaminants, get the best industrial ultrasonic cleaner equipped with a pulse mode. Pulse mode boosts ultrasonic power to 20% on some models to remove stubborn contaminants.
Pulse and sweep cannot operate simultaneously but equipment is available that automatically switches between the two. An example is the Elmasonic x-tra ST series referenced above. The ultrasonic performance is temporarily increased while the even ultrasonic sound field distribution in the bath enhances the cleaning effect.
4. Understanding Ultrasonic Power
When an industrial ultrasonic cleaner is running, electrical power is consumed evenly but it is released in intervals to create the sound waves that shape the ultrasonic signal.
Some manufacturers report ultrasonic peak power, others report average power, and some report both. When comparing equipment you must compare based on the same criterion otherwise you’d be comparing apples with oranges.
While more power usually indicates faster and more effective cleaning, more power is not always better. Too much power can damage electronic parts, the surface finish on a soft metal (e.g. aluminum), and other delicate items.
For cleaning extremely sensitive items, adjustable power is a useful feature. An example is the Elma TI-H series.
Don’t attempt to increase the effective power of an ultrasonic cleaner by under-filling the tank. Ultrasonic cleaner generators that power transducers are tuned to a particular fill level. Operating the unit with less fluid can damage the generator and will result in less than optimized cleaning.
5. Selecting Ultrasonic Cleaning Solutions
The correct cleaning solution chemistry is as important as ultrasonic frequency, power and other points covered in this selection guide.
The vast majority of today’s ultrasonic cleaning solutions are biodegradable, meaning that they reduce or eliminate disposal concerns of the past. They are shipped as concentrates that are diluted with water then mixed in the cleaning tank by running the degas mode.
Our page on industrial ultrasonic cleaning solution formulations provides a useful guide to help you select those that meet your cleaning requirements.
For More Information on Industrial Ultrasonic Cleaners
We have not covered all points to ultrasonic cleaner selection in this post. Please be assured that the professionals at Tovatech are ready to get into the nitty-gritty if you have particularly challenging cleaning requirements.
For questions you have on this or other specification questions contact us at for detailed information.