The Power of Ultrasonic Cleaning Aircraft Engine Maintenance
Maintaining the safety and operational efficiency of aircraft engines is paramount in the aviation industry. For Aviation Maintenance Technicians (AMTs), Aircraft Maintenance, Repair, and Overhaul (MRO) organizations, and airline maintenance facilities, adhering to rigorous procedures outlined in aircraft engine maintenance manuals is non-negotiable. Ultrasonic technology has emerged as a critical tool in this sector, providing significant advantages in both the cleaning of aircraft engine components and Non-Destructive Testing (NDT) operations. This guide explores the diverse applications of ultrasonic energy in aircraft engine maintenance, highlighting its effectiveness and benefits.
Revolutionizing Aircraft Engine Component Maintenance with Ultrasonic Cleaning
Traditional cleaning methods for intricate aircraft engine parts can be time-consuming, labor-intensive, and may not effectively remove contaminants from complex geometries. Ultrasonic cleaning offers a faster, more thorough, and often safer alternative.
Ultrasonic Cleaning Aircraft Generators (IDGs & CSDs)
Integrated Drive Generators (IDGs) and Constant Speed Drives (CSDs) are essential for providing consistent electrical power in aircraft. These units are susceptible to contamination from lubricating oils, metal chips, and carbon deposits, which must be removed during MRO procedures. The complex internal structures of these generators make thorough cleaning a significant challenge.
Ultrasonic cleaning overcomes these challenges through the power of cavitation. The implosion of millions of microscopic bubbles in the ultrasonic cleaning bath effectively reaches all submerged surfaces, rapidly dislodging even tenacious contaminants from intricate internal passages and components.
Tailored Ultrasonic Cleaning Solutions for Generator MRO:
MRO operations can leverage customized ultrasonic cleaning systems for optimal efficiency:
- Large Components (e.g., Housings): For bulky and heavy components like generator housings, large ultrasonic tanks with lifting mechanisms (e.g., cranes) are used. Alkaline-based cleaning solutions are often employed to effectively remove oil, grease, combustion residues, and soot. Agitation of the parts within the solution enhances the ultrasonic action, reducing cleaning times. Elma offers systems with various tank sizes and integrated agitation to suit these needs. These systems can also be combined with rinsing and drying modules for a complete workflow.
- Smaller Internal Components: Benchtop ultrasonic cleaners are ideal for cleaning smaller, more delicate internal generator parts. Key features of these units include:
- Degas Function: Quickly removes trapped air from fresh cleaning solutions, maximizing ultrasonic efficiency.
- Sweep Mode: Ensures uniform distribution of cavitation throughout the bath for consistent cleaning results across all parts.
- Precise Controls: Integrated timers and heaters allow for accurate تنظیم of cleaning cycles and solution temperatures based on specific requirements.
Restoring Jet Engine Fuel Nozzle Assemblies with Ultrasonic Precision
Regular maintenance of jet engines mandates meticulous cleaning and inspection of fuel nozzle manifold adapter assemblies.
The Challenge of Stubborn Carbon Deposits
Baked-on carbon deposits pose a significant cleaning challenge for fuel nozzles. Mechanical cleaning methods often fall short, are time-consuming, risk damaging the precisely machined surfaces, and struggle to reach internal orifices.
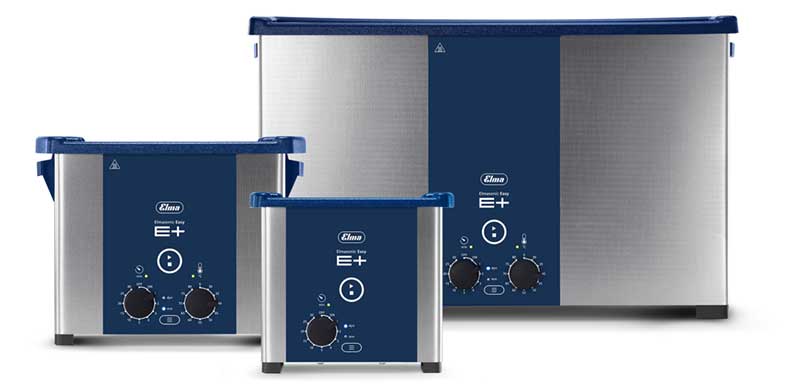
Ultrasonic Cleaning is Highly Effective
Ultrasonic cleaning has proven highly effective in restoring jet engine fuel nozzle assemblies to a like-new condition. Compact tabletop ultrasonic cleaners like the Elmasonic E+ Series (operating around 37 kHz and equipped with a heater, timer, and drain) are commonly used.
Improve Effectiveness of Ultrasonic Cleaner Features
The implosion of billions of microscopic cavitation bubbles provides a powerful yet gentle cleaning action, effectively removing even stubborn baked-on carbon deposits without harming the delicate, highly machined fuel nozzle surfaces. The microscopic size of the bubbles allows them to penetrate intricate internal passages and orifices that are inaccessible to mechanical methods. Features like the continuous sweep mode ensure even cleaning throughout the solution, while a pulse mode can provide extra power for particularly stubborn deposits. Furthermore, ultrasonic cleaning minimizes personnel contact with potentially harsh cleaning chemicals, enhancing safety.
Ultrasonic Cleaning Aircraft Engine Parts is Crucial in Non-Destructive Testing (NDT)
Ultrasonic cleaning is an integral part of NDT procedures for overhauling critical jet engine components, ensuring they meet stringent specifications without compromising their structural integrity.
The Importance of Cleanliness in NDT
NDT methods, such as magnetic particle testing and liquid penetrant testing, rely on the detection of minute surface or near-surface discontinuities. Any residual contaminants can obscure these defects, leading to inaccurate inspections and potentially compromising safety.
Ensuring Accurate NDT Results
Ultrasonic cleaning plays a vital role in both preparing aircraft engine parts for NDT and cleaning them afterward:
- Pre-Cleaning for Inspection: Thorough ultrasonic cleaning of disassembled engine parts by NDT inspectors removes any grease, oil, dirt, or other contaminants that could mask potential flaws.
- Post-Testing Cleaning: After magnetic particle or liquid penetrant testing, ultrasonic cleaning is essential for completely removing all traces of the testing media (magnetic particles or dyes). This ensures accurate quality checks and prevents interference with subsequent maintenance procedures.
- Quality Control of NDT Processes: Regularly cleaning a test panel with known defects using the ultrasonic cleaner verifies the effectiveness of the cleaning process in removing all traces of penetrant dyes, ensuring the reliability of the liquid penetrant inspection line.
Examples of Ultrasonic Cleaners for Cleaning Aircraft Engine Components Using NDT Methods
Benchtop ultrasonic cleaners are well-suited for NDT applications in aircraft engine maintenance. Key features that make these cleaners effective include:
- Precise Temperature and Time Control: Integrated heaters and timers with clear LED displays for accurate تنظیم of cleaning parameters.
- Sweep Mode: Ensures uniform ultrasonic energy distribution for consistent removal of NDT testing media from defects.
- Degas Function: Efficiently removes air from fresh cleaning solutions, optimizing cleaning performance.
- User-Friendly Design: Simple on/off switches for both the unit and the ultrasonic cleaning action.
- Practical Lid: Reduces noise and evaporation, and can be inverted for use as a drain tray for baskets.
Ultrasonic Cleaning Solutions for Aircraft Engine Maintenance
A range of specialized, often biodegradable, ultrasonic cleaning solution concentrates are available, formulated for the specific contaminants encountered in aircraft engine maintenance. These solutions, when diluted with water, offer varying pH levels to effectively address different cleaning challenges.
Proper degassing of fresh cleaning solutions is crucial for optimal ultrasonic cleaning performance. While allowing the unit to run unloaded can achieve this, utilizing a cleaner with a dedicated degas function significantly speeds up the process, particularly in larger tanks.
Regular replacement of the cleaning solution is necessary as contaminants accumulate, reducing cleaning efficiency. Proper disposal of used solutions according to local regulations and thorough cleaning of the ultrasonic tank before refilling are essential maintenance practices.
Contact the Experts for Ultrasonic Cleaning Aircraft Engine Informations
For detailed information on utilizing ultrasonic energy for cleaning aircraft engine components and selecting the ideal ultrasonic cleaning equipment and solution formulations for your specific MRO or NDT needs, call or chat with the specialists at Tovatech. Their expertise can help you optimize your maintenance processes for efficiency, effectiveness, and safety.